Hazard Control & Prevention
A fundamental principle of any good health and safety program is the application of the hierarchy of controls.
At EnHealth we follow the hierarchy of controls and often use a combination of controls when developing the most feasible and effective means of keeping workers safe.
The hierarchy starts with the controls considered to be most effective, and moves to those considered least effective in the following order:
removal of hazard, substitution of hazards
engineering controls
administrative control
personal protective equipment (PPE)
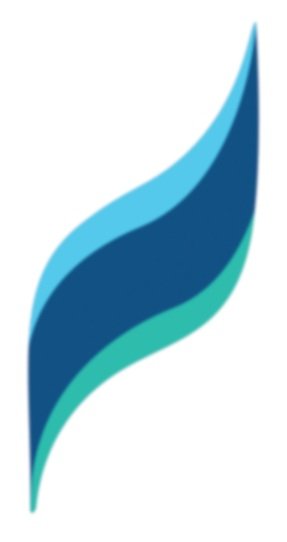
Hierarchy of Hazard Controls
1
Elimination / Substitution Control
Eliminating the hazard completely is always the preferred choice because the hazard is no longer present. Substitution occurs when a new chemical or substance that is less hazardous is used instead of another chemical.
Substitution is sometimes grouped with elimination because, in effect, you are removing the first substance or hazard from the workplace. While these two strategies are the most effective at reducing hazards, they tend to be the most difficult to implement into an existing process or operation. One reason for this, is that the cost to fund the needed research and development to redesign a process may be too high or impractical; however, If the process is still at the design or development stage, elimination and substitution of hazards may be inexpensive and simple to implement by using prevention through design (PtD).
2
Engineering Controls
Engineering controls protect workers by removing hazardous conditions or by placing a barrier between the worker and the hazard.
Examples of engineering controls include installing guardrails to prevent falls, limiting exposure to dust or welding fumes via ventilation, using portable air conditioners to combat heat stress, and installing noise absorption panels to dampen high noise levels. Well-designed engineering controls can be highly effective at protecting workers, and will typically be independent of worker interactions. They typically do not interfere with worker productivity or personal comfort, and make the work easier to perform rather than more difficult.
3
Administration Controls
Administrative and work practice controls involve changes in work procedures, schedules, and training that reduce the duration, frequency, and severity of exposure to known hazards. A work practice control could be a procedure used to control a health hazard, such as, wetting down a concrete surface prior to cutting to reduce the release of respirable crystalline silica dust.
Administrative controls are not mutually exclusive from other safety controls. They are generally used in combination with other controls to reduce employee risk of exposure. For example, additional controls for cutting concrete could include equipping all saws with a shroud and dust collection device, and requiring hearing protection during cutting.
The administration control that ties everything together is training. Training is an important tool for informing workers and managers about workplace hazards and controls so they can work safely and be more productive. Management can install engineering controls and require the use of PPE, but if the worker is not trained on how to perform the work task, use the equipment, or to comply with the safety requirements, then the risk of injury may not be prevented or mitigated.
4
Personal Protective Equipment (PPE)
The final level of the hierarchy is Personal Protective Equipment (PPE). PPE is the least effective protective measure on the hierarchy of controls, but it is still critically important in keeping a safe workplace.
This type of control does not remove the hazard from the work environment and is reliant on proper use by the wearer. For this reason, PPE is not considered a very robust control and should only be used when engineering and administration controls are not feasible or unable to mitigate the hazard to an acceptable level, or as a precaution in case of failure of another level of control. Some examples of PPE include goggles, special clothing, gloves, helmets, and earbuds that a person wears on their body to protect them from a hazard.
Hazard Identification in the Workplace
Prevention through Design
Prevention through design (PtD) addresses occupational safety and health hazards by re-designing or minimizing hazards and risks early in the design phase.
This approach is a way for companies to layout their facilities, equipment, work processes, and more to remove as many hazards as possible. PtD incorporates elimination and substitution early on, and relies less on other controls, such as engineering, administration and PPE, to reduce the risk of injury or illness. PtD typically applies to new operations which are still in the design phase. For existing operations, the hierarchy of controls, starting with engineering controls, remains the best framework for preventing workplace hazards.
Job Safety Analysis
Job Safety Analysis (JSA) is the process of breaking down a job into individual tasks, and then assessing each individual task for potential hazards before a job is performed.
The process focuses on the relationship between the employee(s), the task, the tools, and the work environment. This helps companies take steps to establish engineering controls, safe work practices, and proper training to ensure the hazard can be either removed or mitigated to an acceptable level. The main goal is to prevent injuries by implementing the hierarchy of controls at each step in the work task.
A JSA is typically done when:
A new job is added to the operation.
A job or process is changed.
An accident, injury, or illness has occurred.
A task has a statistically high rate of injury or illness.